FormBox: pre inžinierov a priemyselných dizajnérov
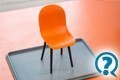
![]() E-booky zdarma |
![]() Školení v oblasti CNC frézek |
![]() ESD inspekce |
Prípadové štúdie pre inžinierov a priemyselných dizajnérov
Skrátenie doby výroby prototypu obalu pomocou FormBoxu a 3D tlače
- vývoj produktu redukovaný z 3 mesiacov na dva dni
- ušetrených 1000 GBP za projekt
Úvod
UTR (Under the Roof) Decorating je kanadská spoločnosť vyrábajúca náradie. Vyvíja, testuje, vyrába a dodáva do maloobchodov po celom svete inovatívny rad produktov pre domáce dekorovanie. Tím UTR vytvára vo svojom vlastnom laboratóriu pre inováciu produktov širokú škálu kutilských produktov inšpirovaných problémami pozorovanými pri práci v teréne.
UTR používa FormBox na prototypovanie svojich dizajnov blistrových obalov. Celý rad produktov UTR je balený v blistroch s podložkou. Pomocou FormBoxu a transparentných foriem Cast Sheet je tím schopný replikovať hromadne vyrábané bristry bez toho, aby opustil internú dielňu. Majú tiež dve 3D tlačiarne, ktoré sa používajú na vytváranie prototypov blistrových obalov. Využitie kombinácie 3D tlače a vákuového tvarovania umožňuje tímu rýchlo vytvárať nové designy a testovať ich s užívateľmi a potenciálnymi zákazníkmi.
"S FormBoxom kombinovaným s 3D tlačiarňami sme dokázali skrátiť dobu vývoja našich oblalov z týždňov na doslova dni." - Under The Roof
Problémy
Zatiaľ čo UTR navrhuje všetky svoje produkty v Kanade, fyzicky sú vyrábané v Číne. V minulosti musel nechávať vyrábať v Číne aj všetky svoje prototypy. Fyzické a kultúrne rozdiely medzi Kanadou a Čínou niekedy spôsobovali oneskorenie vývojovej fázy. Odosielanie prototypov z Číny do Kanady bolo časovo náročné, nákladné a vystavovalo ich potenciálnemu poškodeniu počas prepravy.
Pri vytváraní nových produktov je dôležité zistiť, koľko jednotiek môžu niektorí maloobchodníci zvažovať za prvú objednávku. UTR potom môže robiť presné odhady, koľko jednotiek by si mali objednať z továrne v Číne. Čím lepšia kvalita modelu je pre týchto maloobchodníkov k dispozícii, tým vyšší je počet jednotiek, ktoré musia objednať, čo zase zlacňuje jednotkové náklady UTR.
Riešenie
Vďaka vlastnej výrobe všetkých obalov pomocou 3D tlačiarne a FormBoxu nevznikne pri prechode od myšlienky k fyzickej forme žiadna šanca na chyby. Tým sa úplne odstránila potreba prototypovania v Číne a znížilo sa riziko poškodenia pri preprave, oneskorení alebo nákladných chýb. Po zavedení procesu FormBox + 3D tlač spoločnosť UTR skrátila dobu realizácie vývoja obalov z priemerných troch mesiacov na iba dva dni.
Použitie Cast Sheets umožnilo UTR vytvárať takmer presné jednotlivé repliky navrhnutého blistra. Pomocou nich, určených ako ukážkové príklady nových produktov, mohli maloobchodní kupujúci presne odhadnúť, koľko objednávok môže továreň vyrobiť.
Výsledky
- výrazne skrátená doba vývoja produktu
- zvýšené objednávky od maloobchodníkov
- nižšie náklady na lepšie vzorky
- schopnosť vytvárať kvalitné vzorky
Vývoj prototypov a krátkych sérií produktov s 3D tlačou a formami z FormBoxu
- doba vývoja produktu znížená na tri dni
- úspora 190 GBP za náklady na nastavenie
Úvod
Dean Pankhurst je interdisciplinárny dizajnér, ktorý pracuje v rôznych médiách, ale hlavne v produktovom dizajne a digitálnych médiách. Pracuje v produktovom tíme spoločnosti Mayku a zároveň navrhuje a vyrába pre umelcov a dizajnérov jednorazové akcie, prototypy a malosériovú výrobu. Má prístup k radu nástrojov a strojov a vďaka FormBoxu rozšíril škálu možností, ktoré môže svojim klientom ponúknuť.
Dean pred niekoľkými rokmi dostal nápad na stmievaciu lampu a pomocou 3D tlače a FormBoxu ho nedávno pretvoril na skutočnosť. Všeobecná myšlienka je, že žiarovka funguje aj ako stmievač, ktorý nastavuje jas lampy. Vnútro výrobku tvorí vysokonapäťová doska s obvodmi, ktorá má potenciometer a niekoľko veľkých kondenzátorov.
"FormBox dopĺňa všetky ostatné nástroje, ktoré mám k dispozícii, čo mi umožňuje s istotou vyrábať celý produkt sám, a to nákladovo efektívnym a flexibilným spôsobom." - Dean Pankhurst
Problémy
Dean chcel, aby bol exteriér lampy vyrobený z ťažkého odliateho materiálu, ktorý bude vyzerať ako textúrovaný kameň. Tento druh prírodných povrchových úprav nemôže byť 3D tlačiarňou prevedený presvedčivo. Požadované tesné tolerancie však znamenali, že ručné rezbárstvo alebo sústruženie tiež nebude dobrou voľbou.
Dean ďalej potreboval zaistiť, aby všetky časti do seba správne zapadli. Až potom sa mohol rozhodnúť pre konečný návrh. Testovanie tolerancií a celkového tvaru konštrukcie pomocou odlievacieho procesu, napr. pomocou silikónu, by bolo neúprosne nákladné. Vytvrdzovanie silikónových a polyuretánových foriem navyše trvá veľmi dlho. Pri vývoji nových produktov je dôležité rýchlo iterovať a čo najskôr pokročiť v prototypovaní, aby ste sa na trh dostali čo najrýchlejšie. Čakanie 24 hodín na vytvrdenie veľmi oneskorujú celý proces.
Riešenie
Použitie zliatinových materiálov vám umožňuje otestovať jemné rozdiely v štruktúre a farbe a zároveň kombinovať presnosť a opakovateľnosť digitálnej výroby s hmatateľnejšími a vysoko kvalitnými povrchovými úpravami. Zahrnutie FormBoxu do procesu návrh umožnilo Deanovi rýchlo vyrobiť formy na testovanie aj finálnu výrobu stmievacej lampy.
FormBox je neuveriteľne užitočný na výrobu foriem na prototypovanie odliatkov. Dean sa snaží použiť vákuové tvarovanie, kedykoľvek je to možné, pretože sa zníži náklady na prácu v porovnaní s inými procesmi výroby foriem, ako je silikón alebo polyuretán. Dean potreboval zaistiť, aby do seba všetky súčasti zapadli správne, a zároveň nemal tak vysoký rozpočet, aby mohol dlho testovať tolerancie a celkový tvar konštrukcie pomocou nákladného procesu odlievania.
Šablóny pre formu boli vytlačené na 3D tlačiarni a vytvorené pomocou Cast Sheets za menej ako jeden deň. Dvojdielna forma umožňuje dutý tvar s otvormi na žiarovku a okrajom na základni pre elektroniku. Dean vyrobil niekoľko prototypov zo sadry a štandardného jesmonitu AC100, čím otestoval celú zostavu. Nakoniec pre finálny produkt zvolil jesmonit AC730 v uhlíkovej šedej.
FormBox doplnil všetky ostatné nástroje, ktoré má Dean k dispozícii, čím mu umožnil s istotou vyrobiť celý produkt sám. Navyše nákladovo efektívnym a flexibilným spôsobom.
Výsledky
- schopnosť dosiahnuť prirodzené povrchy pomocou nástrojov na digitálnu výrobu
- významné zníženie nákladov na prototypovanie
- skrátenie doby vývoja projektu
Rýchle prototypovanie s FormBoxom
Theo Ford je oceňovaný londýnsky priemyselný dizajnér. Vytvára produkty pre klientov a potrebuje postupovať rýchlo a držať tak krok s ich plánovaním. Theo prevádzkuje malú dielňu a musí udržiavať nízky rozpoačet. Má malú modelársku zostavu s 3D tlačiarňou, FormBoxom a ďalším základným prototypovým vybavením.
Pomocou FormBoxu môže Theo Ford za pár hodín prejsť z CAD programu až k dávke fyzických prototypov. Vďaka tomu môže ukázať svojim klientom svoje vízie, a to za minimálne náklady. Kombináciou 3D tlače a vákuového tvarovania je Theo schopný za jediný deň hromadne vyrobiť množstvo prototypov.
Theo navyše utratí iba 1 GBP za každý prototyp stoličky, ktorý vytvorí pomocou FormBoxu. Z rozpočtu jeho klienta by bola outsourcingová výroba neúnosne nákladná.
"FormBox je v mojej dielni mocný nástroj. V spolupráci s mojou 3D tlačiarňou dokážem vyskúšať rôzne varianty bez nutnosti dlhej tlače alebo nákladného outsourcingu výroby." - Theo Ford
Problémy
Theo bol požiadaný novým co-workingovým priestorom o návrh sady zákazkového nábytku pre novú lokáciu v Londýne. Prvou výzvou bolo vytvorenie sady stoličiek, ktoré by zodpovedali škandinávskemu štýlu. Rozpočet bol napätý a klient bol veľmi konkrétny. Theo chcel svoj nábytok vymodelovať, aby klientovi mohol svoju víziu predniesť.
Riešenie
Najprv vytvoril farebnú schému a návrhový jazyk pre priestor, potom začal s náčrtom variácií. Theo chcel pre klienta vymyslieť niekoľko nápadov a materiálnych úprav. Časové a rozpočtové obmedzenia znamenali, že tlač 10 variantov stoličiek nebude možná. Svoje nápady teda navrhol ručne a vymodeloval formu stoličky v Solidworks. Potom pomocou svojej 3D tlačiarne vytvoril hlavnú šablónu. Na vykonanie niekoľkých variácií svojho dizajnu využil FormBox.
Theo rýchlo zhotovil 10 identických kópií škrupiny stoličky, vyrezal ich skalpelom a každú nastriekal inou farbou. Na niekoľkých kusoch použil texturačný základ. Experimentoval s matnými a lesklými povrchmi a vyskúšal rôzne odtiene farieb a hrúbky materiálu. Ďalej Theo vytlačil jednu sadu nôh, aby mohol predviesť návrh stoličiek v celej ich krásnej. Klient prišiel do štúdia a ihneď bol na Theovom zmenšenom modeli priestoru schopný vidieť, ako rôzne povrchové úpravy fungujú. Spoločne sa rozhodli pre farebnú schému a stanovili kolektívny smer dizajnu sady stoličiek.
Výsledky
- 10 rôznych variantov stoličiek za minimálne časové a finančné náklady
- rýchla vizualizácia designu
Kategórie produktov
![]() |
Vákuové formovacie stroje |
![]() |
Termofólie |